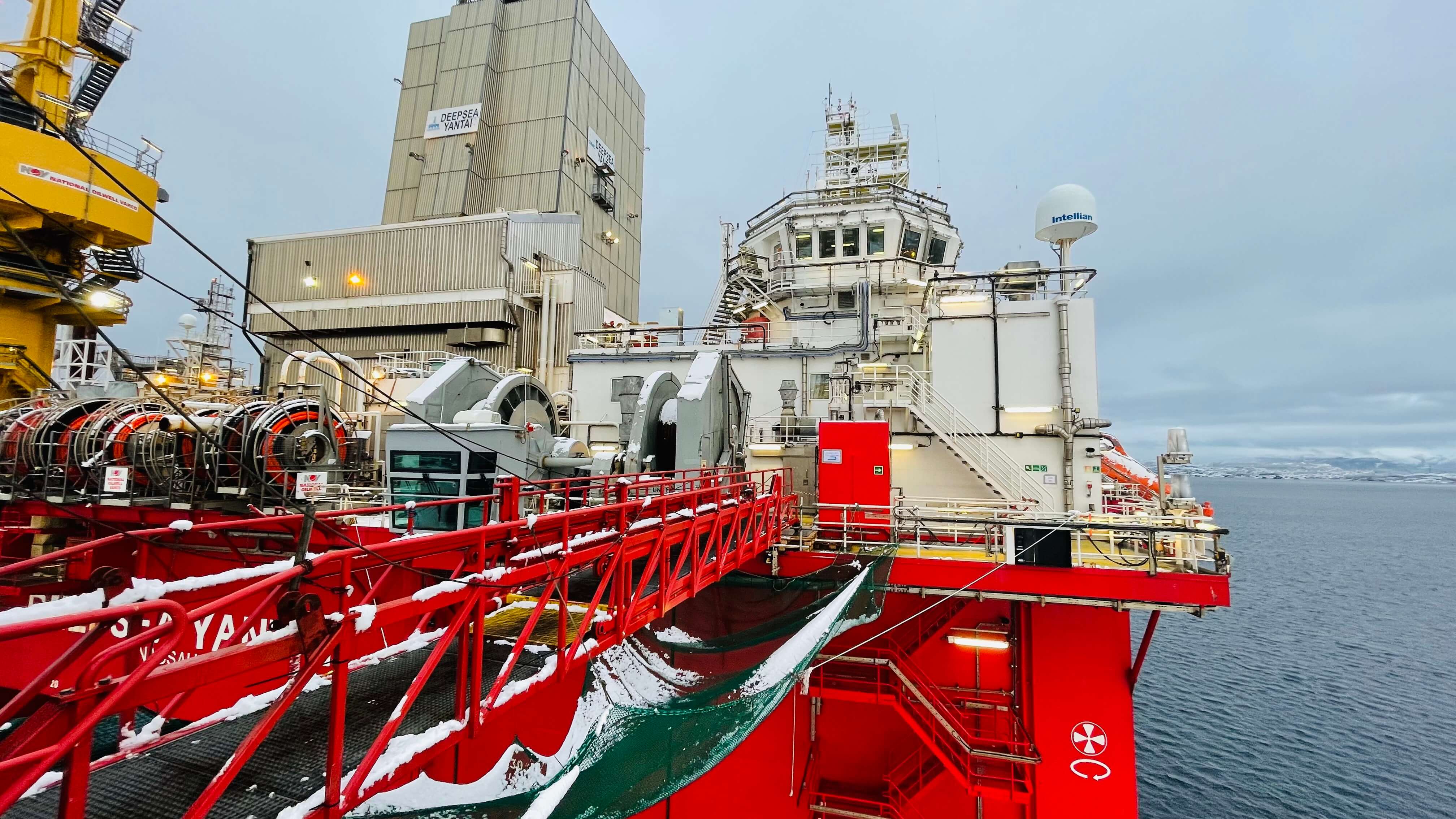
Lifting Operations Manual and Local Procedures:
Review the lifting operations manual and local procedures to ensure they align with NORSOK R-003, LOLER, and other relevant regulations.
Evaluate the clarity and comprehensiveness of procedures for various lifting operations.
Planning of Lifting Operations:
Assess the planning process for lifting operations, including risk assessments, equipment selection, and communication of plans to relevant personnel.
Safe Use of Lifting Equipment:
Verify that lifting equipment is used safely, adhering to manufacturer guidelines, inspection requirements, and proper maintenance practices.
Lifting of Personnel:
Evaluate procedures for lifting personnel, ensuring compliance with safety regulations and industry best practices.
Use of Different Lifting Appliances:
Audit the use of various lifting appliances (cranes, hoists, winches, etc.), ensuring proper operation, maintenance, and operator competence.
Critical Lifting Operations:
Examine procedures and risk assessments for critical lifting operations, such as heavy loads, complex lifts, or lifts in challenging conditions.
Marine Lifting Operations:
Review procedures and safety measures for lifting operations involving marine equipment or personnel transfer between the MODU and support vessels.
Roles and Responsibilities for Maintenance:
Assess the roles and responsibilities of personnel involved in the maintenance of lifting equipment and lifting operations, including record-keeping and reporting.
Training and Emergency Operations:
Verify that personnel involved in lifting operations are adequately trained in safe practices, emergency response, and evacuation procedures.
Enterprise of Competence (EoC) Follow-Up:
Review the implementation and effectiveness of the Enterprise of Competence (EOC) system, ensuring continuous improvement and compliance.
Tagging of Lifting Equipment:
Audit the tagging and labeling of lifting equipment to indicate inspection status, load capacities, and other relevant information.
Record Keeping and Documentation:
Evaluate the documentation of lifting equipment inspections, maintenance, and operational records, ensuring proper documentation practices.
Communication and Reporting:
Assess communication channels for reporting lifting equipment issues, near-misses, incidents, and maintenance needs.
Competence and Training:
Review the training programs and competency assessments for personnel involved in lifting operations and equipment maintenance.
Lifting Operations Manual and Local Procedures:
Review the lifting operations manual and local procedures to ensure they align with NORSOK R-003, LOLER, and other relevant regulations.
Evaluate the clarity and comprehensiveness of procedures for various lifting operations.
Planning of Lifting Operations:
Assess the planning process for lifting operations, including risk assessments, equipment selection, and communication of plans to relevant personnel.
Safe Use of Lifting Equipment:
Verify that lifting equipment is used safely, adhering to manufacturer guidelines, inspection requirements, and proper maintenance practices.
Lifting of Personnel:
Evaluate procedures for lifting personnel, ensuring compliance with safety regulations and industry best practices.
Use of Different Lifting Appliances:
Audit the use of various lifting appliances (cranes, hoists, winches, etc.), ensuring proper operation, maintenance, and operator competence.
Critical Lifting Operations:
Examine procedures and risk assessments for critical lifting operations, such as heavy loads, complex lifts, or lifts in challenging conditions.
Marine Lifting Operations:
Review procedures and safety measures for lifting operations involving marine equipment or personnel transfer between the MODU and support vessels.
Roles and Responsibilities for Maintenance:
Assess the roles and responsibilities of personnel involved in the maintenance of lifting equipment and lifting operations, including record-keeping and reporting.
Training and Emergency Operations:
Verify that personnel involved in lifting operations are adequately trained in safe practices, emergency response, and evacuation procedures.
Enterprise of Competence (EoC) Follow-Up:
Review the implementation and effectiveness of the Enterprise of Competence (EOC) system, ensuring continuous improvement and compliance.
Tagging of Lifting Equipment:
Audit the tagging and labeling of lifting equipment to indicate inspection status, load capacities, and other relevant information.
Record Keeping and Documentation:
Evaluate the documentation of lifting equipment inspections, maintenance, and operational records, ensuring proper documentation practices.
Communication and Reporting:
Assess communication channels for reporting lifting equipment issues, near-misses, incidents, and maintenance needs.
Competence and Training:
Review the training programs and competency assessments for personnel involved in lifting operations and equipment maintenance.